The OECD report MAKING LIFE EASIER, RICHER AND HEALTHIER: ROBOTS, THEIR FUTURE AND PUBLIC POLICY published by OECD SCIENCE, TECHNOLOGY AND INDUSTRY POLICY PAPERS, No. 117 July 2021. The paper is written by Alistair Nolan, a Senior Policy Analyst in the OECD’s Directorate for Science, Technology and Innovation. It is a follow up to the three year OECD program “The Next Production Revolution: Implications for Governments and Business”. Link to full report is found here
Section 4. Current and emerging uses of robots
This section reviews the main current and emerging uses of robots. These include uses in industry, agriculture and services, as well as space, the oceans, and education. Owing to the COVID-19 pandemic, and the potential for robots to ameliorate this or future contagions, particular attention is given to robots in healthcare. Below text is extrated from page 25 to 27 in the report.
Can newer industrial robots help SMEs to automate?
In all countries, most manufacturers are SMEs. SMEs work exclusively with “small series manufacturing” (production runs yielding few units). This results in uneven and low utilization of machines, which reduces profitability. Most SMEs in manufacturing use manually operated machines. While many SMEs wish to automate, it is difficult to do so profitably when product volumes and product types change frequently and robots are fixed (i.e. anchored to a factory floor). Costs also increase if, under such varying conditions, robots have to be repeatedly reprogrammed. Fixed robots typically use fences for worker safety. However, in terms of efficiency alone, fences can create problems if small series manufacturing means that robots need frequent retooling. All of the above factors have led to extremely low automation rates among SMEs in manufacturing, perhaps less than 1% (or around 10 robots per 10 000 employees, compared to 1 100 to 1 400 robots per 10 000 employees in the automotive sector).
Because many customers want greater freedom of choice over product configurations, and global competition is intense, the need for more flexible and future-proof automation is also felt by large manufacturers. For example, in the automotive, electronics and white goods industries, a growing number of large firms have shortened production runs and expanded product mixes. Some large firms have also found themselves locked into the use of traditional fixed robot units with fences, with difficulties to adapt these for new products or to change factory layouts. All of these conditions raise demand for more flexible and future-proof robot solutions. In this connection, firms in many industries have five common needs:
- Rapid robot integration and installation, reduced from weeks to days, to speed conversion and avoid lost production.
- Rapid production scale-up and scale-down, to more quickly amortise investments and adjust production volumes.
- Flexible robot configurations and fast programming, to adjust production processes quickly to new products, and to mix products on the same machine.
- Easily changed layout without fences, to quickly move production lines and avoid being locked into a given factory layout.
- Future-proofed and standardised robot solutions, to be able to reuse robots easily as product mixes change, employing flexible but standardised solutions. Mobile robots help to provide such flexibility.
Table 1. describes the three generations of industrial robot to date. Each generation has
emerged to help address the evolving needs of industry described above
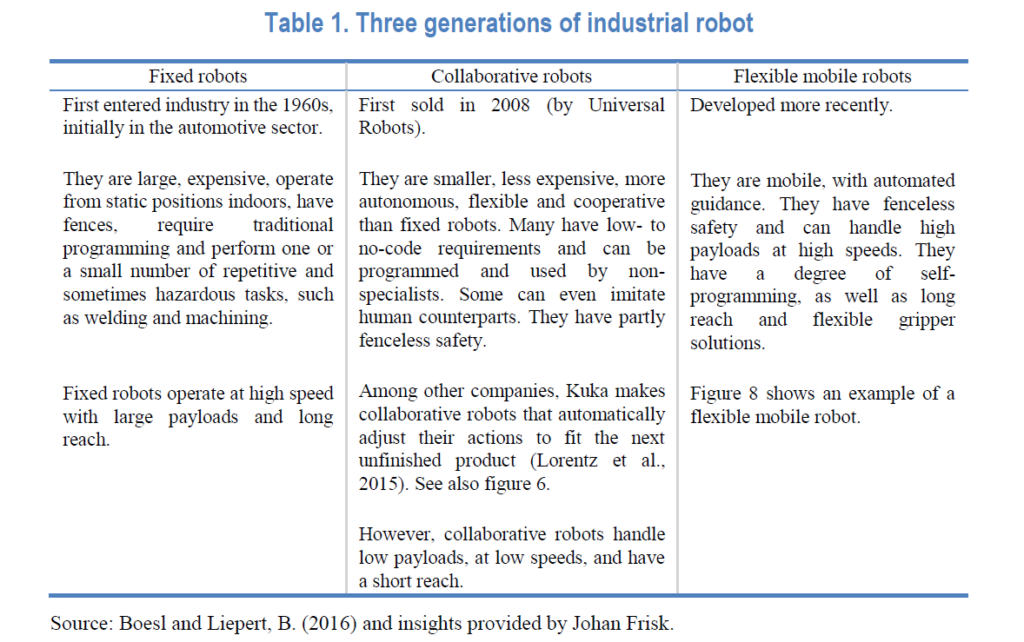
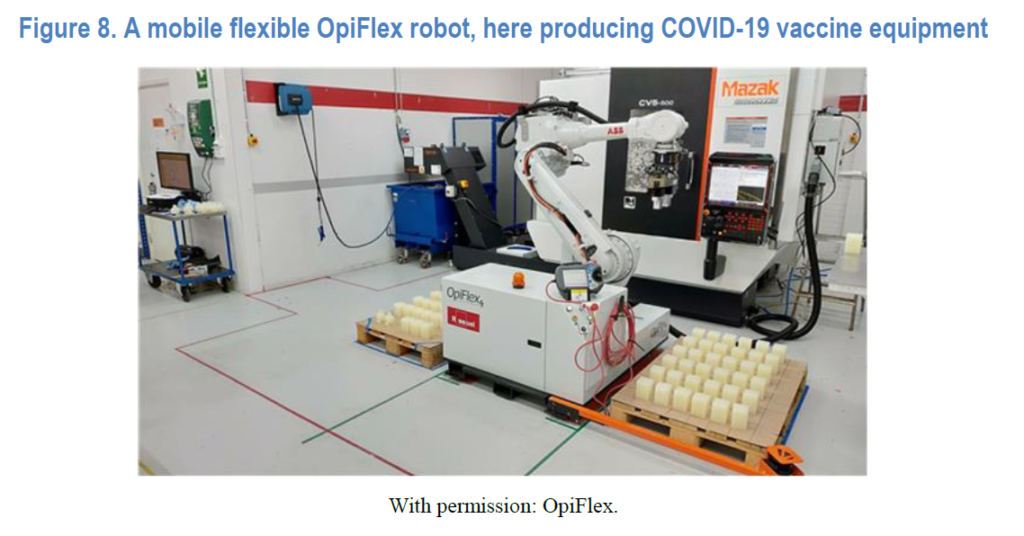
Figure above “Figure 8. A mobile flexible OpiFlex robot, here producing COVID-19 vaccine equipment” from report